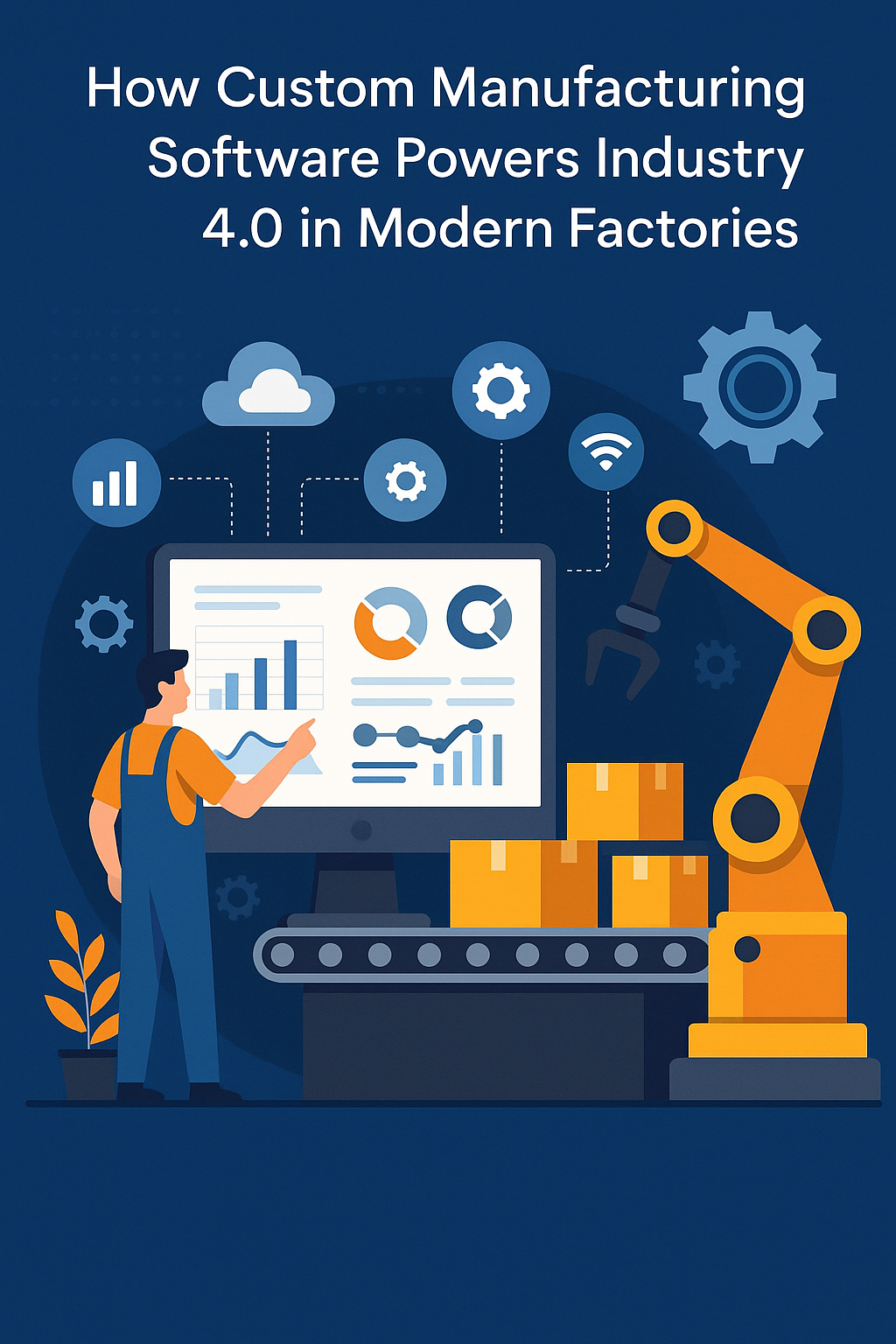
How Custom Manufacturing Software Powers Industry 4.0 in Modern Factories
Step inside a modern, future-ready factory and you’ll notice something remarkable: machines making split-second decisions, production lines adapting on the fly, and data streaming in real-time. This isn’t science fiction—it’s the reality of Industry 4.0.
While the promise of digital transformation is huge, many manufacturers still struggle to align outdated systems and rigid workflows with the dynamic demands of today. This is exactly where Custom Manufacturing Software plays a vital role.
Backed by robust ERP solutions, custom software is helping manufacturers bridge the gap between traditional operations and a connected, intelligent future—one where speed, scalability, and precision are the new standard.
Understanding Industry 4.0 and Its Shift in Manufacturing
Industry 4.0 marks the fourth wave of the industrial revolution. It brings together digital technologies and classic manufacturing practices to create smarter, more adaptive environments. In this new model, machines, devices, and systems are interconnected. They collect and share data in real time and respond instantly to changes.
The results? Improved efficiency, fewer delays, and the ability to deliver more personalized products—without sacrificing speed or scale.
Why Custom Manufacturing Software Is the Backbone of Industry 4.0
While the vision of Industry 4.0 is clear, its execution depends heavily on having the right software in place. Off-the-shelf platforms often fall short when it comes to supporting complex, industry-specific workflows. That’s where tailored solutions come in.
Built to Fit Your Factory
Custom Manufacturing Software is developed around your existing processes, tools, and team. It adapts to your environment—instead of forcing your factory to adapt to it. That means smoother adoption, better integration, and far less operational friction.
Connecting Legacy Systems with Modern Technologies
Many factories still rely on legacy equipment and software. Replacing them outright isn’t always feasible, especially for established businesses. Custom software provides a bridge—making it possible to integrate modern sensors, IoT platforms, or analytics tools with the infrastructure you already use.
This seamless connection enables manufacturers to evolve without disrupting ongoing operations.
Real-Time Data for Faster, Smarter Decisions
In manufacturing, every second counts. Custom software gives plant managers and operators access to real-time dashboards that reflect current performance, machine status, and production flow.
With this visibility, decisions can be made instantly—helping teams correct inefficiencies, reduce downtime, and maintain high output quality without delay.
Designed to Grow with Your Business
As your production grows or changes, your systems need to keep up. One-size-fits-all solutions often hit a wall when you expand to new lines or markets.
Custom Manufacturing Software is built to scale. It allows you to add new capabilities, integrate third-party tools, and reconfigure workflows quickly. This kind of flexibility ensures your operations stay responsive to demand shifts or technological advances.
ERP: The Central Engine of Industry 4.0
Enterprise Resource Planning (ERP) systems have always supported core manufacturing functions like inventory, procurement, and financials. But in the age of Industry 4.0, they’ve evolved into something more.
Today’s ERP platforms integrate with IoT devices, handle real-time analytics, and even support predictive maintenance. They help automate repetitive tasks, streamline production planning, and track resource usage with pinpoint accuracy.
When combined with custom software, ERP systems become even more powerful—turning factories into data-driven powerhouses.
Tangible Benefits of Custom Software in Manufacturing
The advantages of custom-built software aren’t just theoretical—they’re measurable. Manufacturers who implement it gain:
- Improved Efficiency: Automation of routine tasks frees up teams for higher-value work while reducing human error.
- Better Product Quality: With real-time monitoring, defects can be caught and corrected on the spot.
- Cost Savings: Predictive maintenance, optimized workflows, and smarter resource use lower operational costs over time.
Tackling the Challenges of Custom Integration
No digital transformation journey is free from obstacles. When introducing new software, manufacturers often face:
- Data security concerns
- Integration with older systems
- Training and change management needs
But these challenges are manageable with a solid roadmap and the right implementation partner. Manufacturers who approach digital adoption with a clear strategy see smoother transitions and faster returns on investment.
The Way Forward: Embrace, Adapt, Lead
Industry 4.0 isn’t a distant goal—it’s happening now. And to compete in this new era, manufacturers need to move beyond off-the-shelf solutions and embrace custom software that fits their specific needs.
Custom Manufacturing Software acts as the enabler of digital transformation. It equips manufacturers with the tools to optimize, adapt, and lead in a constantly evolving industry.
From real-time visibility and integrated systems to smarter workflows and lower costs, the benefits are too significant to ignore.
In short, if you’re serious about staying competitive in the age of Industry 4.0, the path is clear: integrate smarter, innovate faster, and lead with confidence.