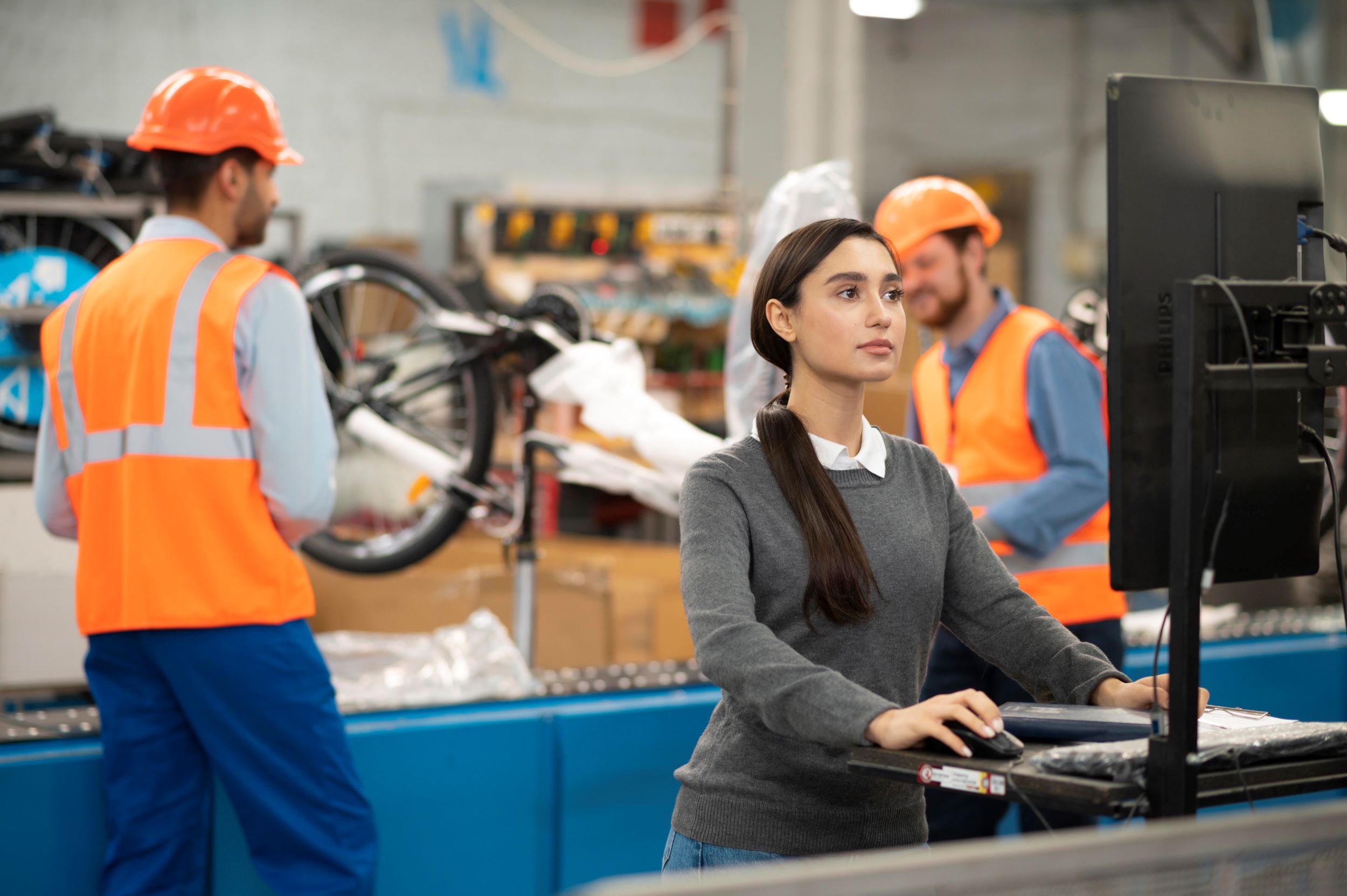
Smart Cost Management with Manufacturing ERP Software
In manufacturing, wasted materials and production delays can quickly drain profits. Reducing costs isn’t just about spending less—it’s about working smarter. That’s where manufacturing ERP software from FINAC makes a difference. It helps businesses track inventory, streamline processes, and use resources more efficiently. No more guesswork, no more waste—just smooth operations that save time and money.
But how exactly does it help manufacturers reduce expenses and increase profits? Let’s break it down.
How Manufacturing ERP Software Saves Money and Increases Profits
1. Minimizing Waste and Material Costs
Manufacturing requires precise planning. Excess inventory leads to waste, while shortages cause costly delays. With real-time inventory tracking, manufacturers can balance supply and demand more effectively. Manufacturing ERP software prevents overstocking, ensures materials are used efficiently, and automates reordering to avoid last-minute, high-cost purchases. This keeps operations running smoothly and prevents unnecessary expenses.
2. Maximizing Workforce Productivity
Labor is one of the biggest expenses in manufacturing. Without proper management, tasks get misassigned, overtime costs rise, and productivity drops. A structured system helps businesses assign tasks effectively, reduce manual work, and track employee performance. The result? A more efficient workforce, fewer unnecessary labor costs, and higher overall output.
3. Improving Production Workflow
Missed deadlines don’t just delay orders—they lead to higher costs, wasted resources, and frustrated customers. A well-organized system keeps production on schedule by identifying potential issues before they cause disruptions. With smarter scheduling and automated tracking, businesses can reduce downtime, prevent bottlenecks, and keep production running efficiently. On-time deliveries and fewer errors mean higher customer satisfaction and improved profitability.
4. Smarter Financial Planning
Tracking expenses manually often leads to errors, budget mismanagement, and financial uncertainty. Manufacturing ERP software provides clear financial insights, helping businesses see exactly where money is going. It simplifies cost tracking, prevents overspending, and ensures that every penny is used wisely. With better financial control, manufacturers can cut unnecessary expenses while maintaining stable growth.
5. Strengthening Supplier and Customer Relationships
A smooth supply chain is crucial for cost-effective manufacturing. Late deliveries, inconsistent suppliers, or communication gaps can slow down production and increase costs. A well-integrated system ensures seamless coordination between suppliers, manufacturers, and customers. When orders arrive on time and production stays on schedule, businesses can avoid unexpected expenses and build stronger relationships with their partners and customers.
6. Ensuring Compliance and Reducing Regulatory Costs
Manufacturers must meet strict quality and regulatory standards. Failing to comply can lead to fines, legal issues, or product recalls—each of which can severely impact profits and reputation. Manufacturing ERP software helps track compliance requirements, manage audits, and ensure quality control. Staying ahead of regulations prevents costly mistakes and protects long-term business success.
Conclusion
Managing a manufacturing business comes with many challenges, but cutting costs shouldn’t be one of them. A smart system helps reduce waste, improve efficiency, and keep operations running smoothly. FINAC ERP provides manufacturers with the tools they need to stay in control, optimize costs, and increase profits.